Lamellophone
Boston University | Candidate for M.S. in Product Design & Manufacture | Spring 2024
OBJECTIVE
Design and produce 10 identical assemblies of a functional lamellophone. The objective is not necessarily to create a novel design, but to select appropriate production processes and understand what it takes to create multiples of a product in spec at the production level.
SKILLS SNAPSHOT
DFM/DFA
ONSHAPE
COST ANALYSIS
MATERIAL SELECTION
PRIOR ART RESEARCH
VOICE OF THE CUSTOMER RESEARCH
FINITE ELEMENT ANALYSIS (FEA)
SHEET METAL BENDING
ENTERPRISE CONTENT MANAGEMENT (ECM)
DESIGN STEPS
-
Reached out to a subject matter expert Bart Hopkin to obtain a copy of his book Making Lamellophones and took notes which informed specifications
-
Established the team's Enterprise Content Management (ECM) strategy
-
Wrote product specifications including size, weight, and tuning for each key
-
Did sheet metal bending of keys and retention clip for first prototype, then helped design and troubleshoot the wire EDM'd die in further iterations
-
Did all material selection analyses in ANSYS Granta
-
Conducting EVT, DVT, PVT, and Mass Production (MP) cost analyses in aPriori
-
Performed FEA analyses in ANSYS Mechanical Workbench to prove the life of the keys would be sufficient per our requirements
-
Wrote 5 SOPs and 5 process plans for four parts and the assembly
-
Created EVT, DVT, PVT, and MP presentations
-
Designed a tuning fixture to cut down on assembly time

An initial sketch of a concept I proposed


Photos of the team's first successful prototype





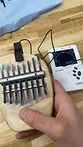
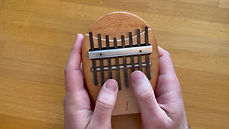


Tuning fixture I designed, in CAD and in use! It helps set the lengths of each key.
RESULTS
-
11 functional, identical, tuned prototypes!​
-
1 Wire EDM'd die and 1 FDM 3D-printed tuning fixture
-
Cost analyses including material cost, labor cost, and machine time for all parts, assembly processes, accessories, and packaging
-
FEA proving the expected life aligns with our specifications
-
The final product is being used as an example for the course moving forward, and it is displayed in the College of Engineering building!
.jpg)
10 completed PVT units!
"I literally thought you bought this"
- User Tester 1
​
"I'm not kidding, this is the happiest I've ever been"
- User Tester 2
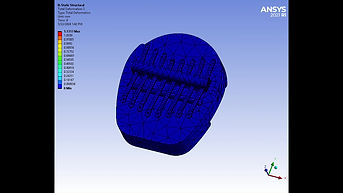
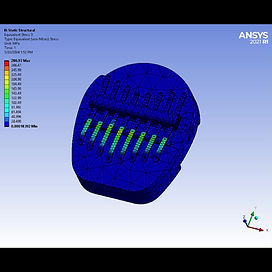
FEA done in ANSYS Mechanical Workbench:
Top: deformation as keys are they are bent
Bottom: Stress on keys bent over the anchor bar
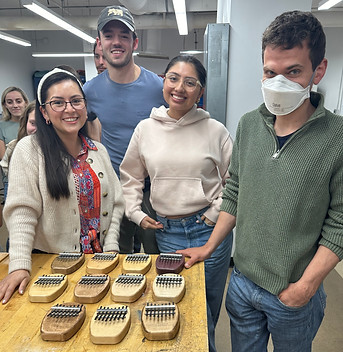
Four team members with 11 PVT units!

Posing with the display unit in the College of Engineering building!
The final presentation I created, which our group presented on the last day of class.